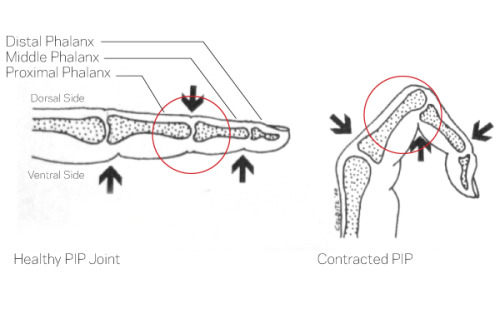
Contracture of the PIP joint, a common condition where the tendons in the hands shorten and become stiff, is painful can lead to functional limitation. The typical treatment is surgery followed by splinting, but current splints are painful and ineffective and therefore usually patients do not improve after surgery. As part of a collaboration between the Human Engineering Research Lab and the Department of Veterans Affairs I worked with a surgeon, occupational therapists, and engineers to design a splint for the treatment of these contractures.
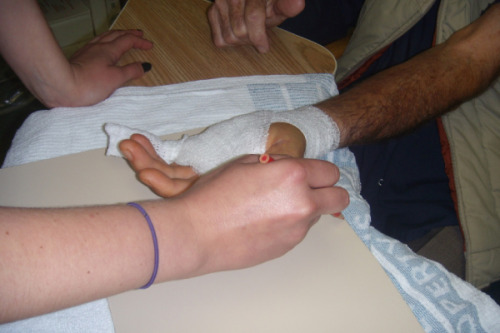
To research the project I spent several days a week in the VA hand clinic observing and interviewing therapists, patients and surgeons.
I also did a literature review and detailed study of splints available on the market, looking at their designs and functional problems.
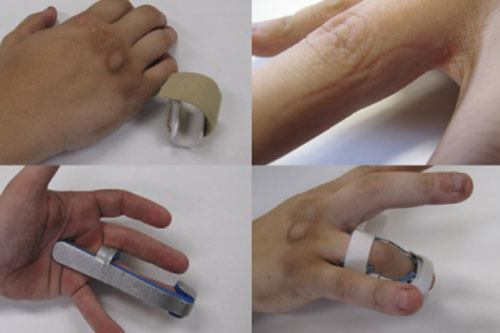
Issues:
Adherence
If the splint is uncomfortable or difficult to put on, it will not be worn
Straightening
Splint needs to apply enough corrective force to straighten the contracture
Fit
Custom splints are difficult to fabricate, off-the-shelf splints are difficult to fit
Comfort, Health
Splints cause pain and discomfort because pressure is uneven
Criteria:
1. Flexible Material combined w/ effective extension moment (Straightening)
2. Low profile, not interfere with activities of daily living (Adherence)
3. Comfortable, held in place by circumferential tension (Adherence, Comfort)
4. Form fitting for variety of finger sizes and still easy to don (Adherence, Fit)
5. Pressure diffused over the whole finger (Adherence,Comfort)
6. Permit visual monitoring of skin health and circulation (Adherence, Comfort)
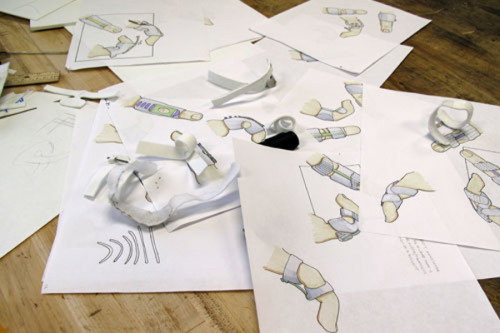

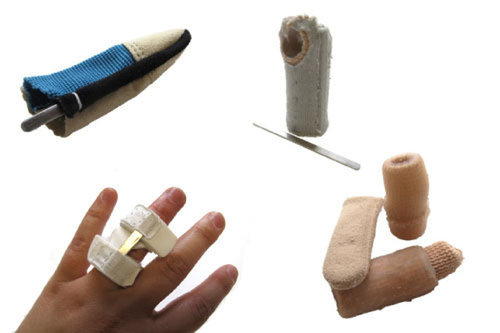
These are some of the many sketches and models I made to explore the form and function of the splint. At first the lab wasn't expecting me to want to make sketch models so I made them out of post-it notes. Eventually I got some craft supplies and silicone tubes and things really took off.
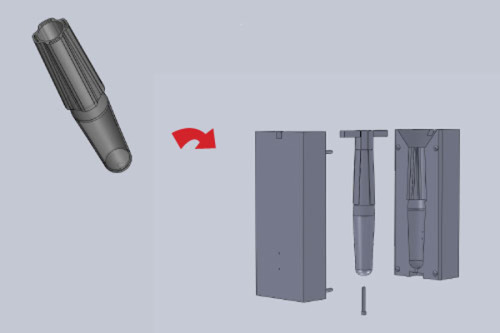
We decided it was best to use cast urethane rubber, so when it was time for "real" prototypes I worked in CAD. I made the splints I wanted to try out then made them into negatives.
I used the SLA machine (a rapid prototyper) to make the CAD models into molds to cast rubber into, then poured the splints and tested them out.
As you can see, there were lots of issues to work out, such as fit and wall thickness. Eventually the molds got more complicated with more features to help the splints come out consistently.
The design we settled on was one where the splint rolls over itself to slide onto the finger easily and painlessly. After it is on stiff batons could be inserted to straighten the joint. It was my belief that by shaping the splint in a curve the plastic alone would be enough and we could do without the batons. After I left, that's what they decided to do.
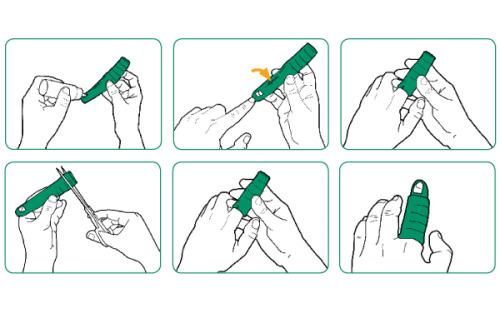
The final splint was finished by my collaborators after my internship ended. I helped them finish up the packaging when I returned to work for them again. There is a U.S. Provisional Patent filed for the splint, and I am a co-inventor.